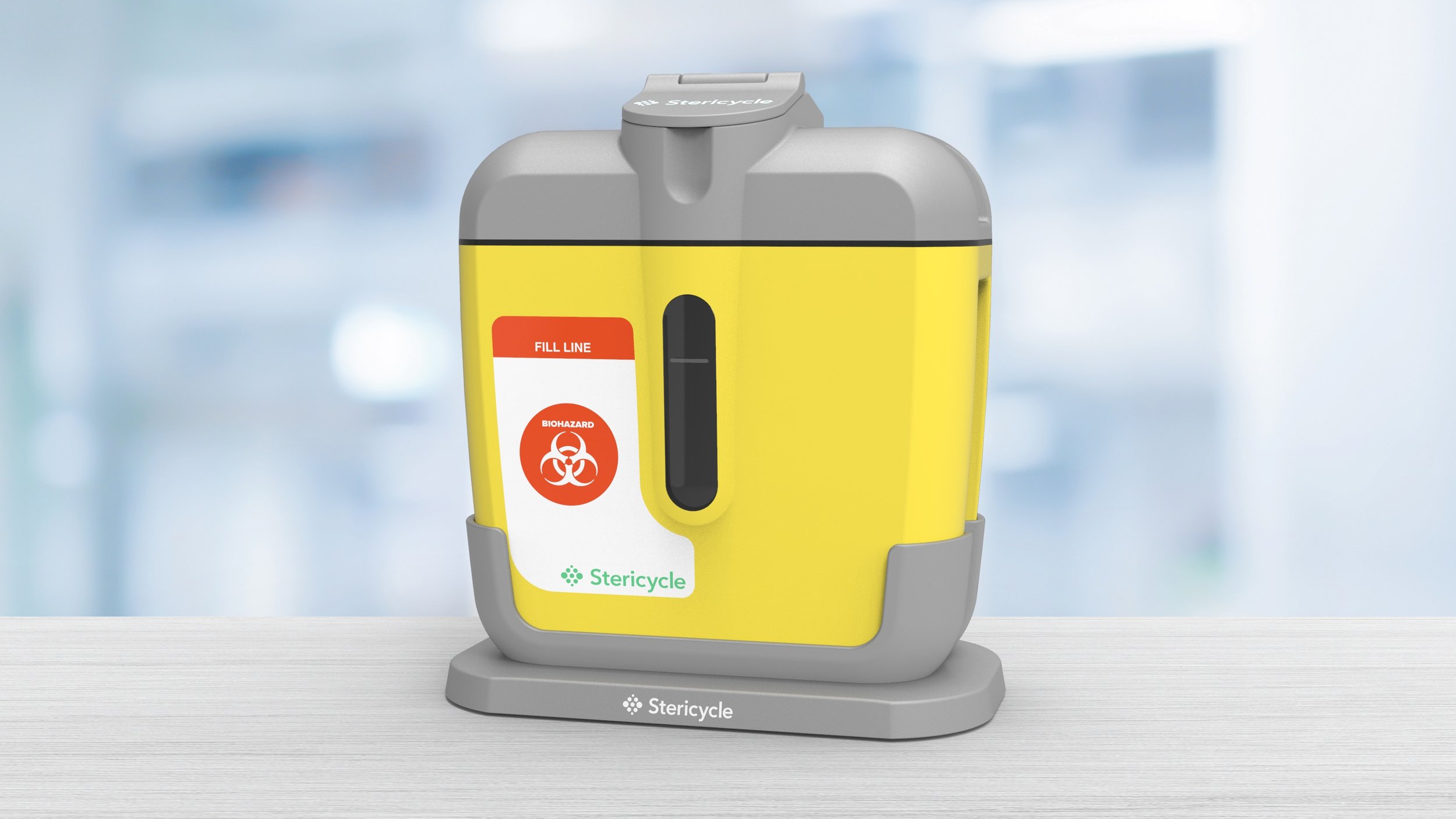
Designing and engineering the next generation of SHARPS containers.
Where it started…
Requirements
Product Requirements
Container and lid must be easily integrated into current wash system robotics
Should have similar design/aspect ratio as current Stericycle containers
Containers should mount to vertical wall via a bracket and be removed horizontally
Bracket should allow for easy cleaning and have a locking feature
Table mount solution required to prevent tipping
Two types of lids needed- raised vertical drop and larger horizontal
Base colors required- yellow, red ,blue
Require marketing IML label on front- IML barcode label on other sides
Meets all requirements of ISO/CSA
One lid assembly fits both 2 and 4 gallon
Uses same clips as current containers
Similar design/aspect ratio
Leak Proof
ISO/CSA Requirements
Must be leak resistant when tipped over and for transport
Must not rupture or leak when dropped from 3.5 ft
Must have integral aperture closure and have temporary and permanent locking feature
Must have clear window for “full” status
Must have integral handle
Must have permanent IML labels
Must have one-handed disposal of sharps
Must withstand 500 wash cycles and life cycle testing
Must prevent overfilling and accidental sticks
Must pass sharps puncture test
Must have mounting system to vertical wall
Container volume vs. “full” volume analysis
Understanding the Product’s Lifecycle
Automated washing and waste management
Competitive Analysis
Inspiration and Preliminary Concepts
Design drivers:
Iconic aesthetic
Cohesive form integrates lid and container
Sealing strategy embraced as brand element
Repeatable form language can be applied across products in line to ensure consistency
Reusable clips for lid
Integrated handle
Visual Messaging
The Chosen One…
Messages Stericycle’s vertical drop ceremony via cylindrical form and window
Contemporary, asymmetric label accentuates drop zone
Approachable, rounded forms embrace manufacturability and cleaning challenges
Cylindrical element (as cutout) becomes the affordance for the handle/ mounting feature
Flat front/back with rounded edges create a friendly design solution while also maximizing the volume of the container
Window in back used for the smart bracket/ level sensing
Designing a Family
Different lids for different functions
Common lids for 2 and 4 gallon containers, and 8 and 17 gallon containers. 3 different drop hole sizes needed with locking tops (and mechanical override).
Different sizes for different uses
4 different sized containers, 2,4,8, and 17 gallon.
Bio-hazard safety
All lids need to be disassembled by a robot. New designs needed to use existing robotic mechanisms and actuation points.
Engineering for Production
Mounting Solutions
Redefining wall and horizontal mounting
2 and 4 gallon containers can be wall mounted or surface mounted. 8 and 17 gallon containers sit in a dolly or on the floor.
Smart Wall Bracket
Passive Overfill
The big idea.
Safety: The design must physically prevent accidental and intentional access to waste
Sensing of Waste: Mechanisms must “tell” the product it's full without electronics
Triggering: The product must “passively” (unprompted by the user) react when it's full
Physical Barrier: This sensing and triggering must activate a method of preventing further insertion until the product is reset
Capping: A separate feature must be closed periodically to seal the product for transport and locked when appropriate